At pleased hour in Mittersill, Austria, a bunch of skiers stroll right into a bar.
The bar is the Platzhirsch, to be actual—a small, wood-adorned watering gap barely greater than a tiny home. The skiers are a handful of business people who—in varied capacities—construct, promote, market, evaluation, analyze, and breathe snowboarding. They simply accomplished a tour of the ski manufacturing facility a quarter-mile up the hill, the place a black Blizzard brand blazed onto a white tower dominates the Mittersill skyline.

We cozy as much as a live-edge desk with a sales space. Any person says, “Rattling, that was spectacular.” Tall bottles of lager clink.
Mittersill’s heartbeat has pulsed snowboarding since earlier than 1945, when Anton Arnsteiner returned from battle and began making skis in his household’s workshop. Lower than a decade later, the Blizzard model launched snowboarding’s first polyethylene bases plus steel and fiberglass layups. Quick ahead 70 years and a slew of improvements, and the Mittersill manufacturing facility cranks out tens of hundreds of pairs of skis annually. A complete North American market calls for freeride fashions (responsible!). A second manufacturing facility in Ukraine fills European rental- and package-ski quotas. The barn-looking constructing adjoining to the manufacturing facility, which homes Blizzard’s race-focused operation, is so shrouded in secrecy that it looks like we positively shouldn’t discuss Battle Membership. And guys like Stefan Moser (Blizzard’s lead ski designer), Gianluca Bisol (Worldwide product supervisor), and Steiner Thornsten (Blizzard’s advertising lead for Germany, Switzerland, and Austria) tackle a celeb high quality.

By the point we’ve devoured (one other) Schnitzel dinner and Bisol begins his five-hour commute again dwelling to Italy, I’m stewing on just a few takeaways as I order a final Weissbier. For one, set towards the backdrop of Europe’s ski historical past, I really feel tinier than a stellar dendrite. Two, we typically take large manufacturers without any consideration, lumping all of them collectively in a conglomeration of mass-produced items; Blizzard’s operation is outlined by a labor-intensive consideration to element that prioritizes hands-on high quality management and teamwork over reducing corners. And three: I want to return again right here to ski once more.
Right here’s a set of the sights from Blizzard HQ:

When Bisol turned the Anomaly and Black Pearl skis inside out, it drove dwelling the model’s consideration to element. It’s no small job to switch basic skis just like the Brahma and Bonafide, they usually didn’t take the ordeal calmly. Learn concerning the new skis in our 2025 Blizzard Skis Preview.


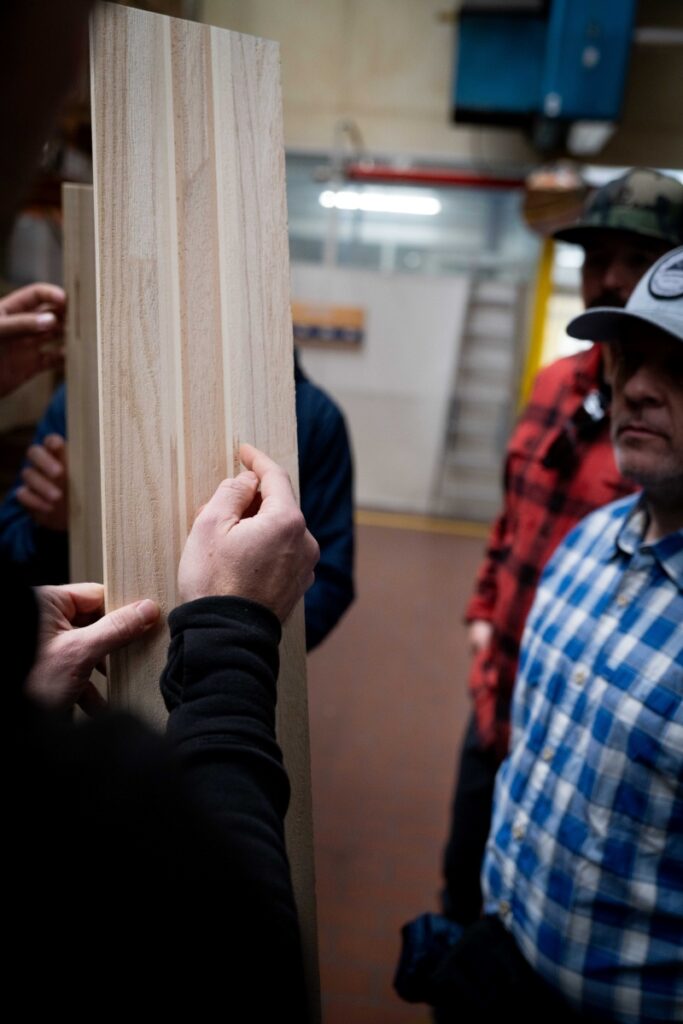
Blizzard’s proprietary True Mix woodcore consists of intricately positioned strips of assorted wooden varieties, that are sourced sustainably within the Alps. I used to be struck by how engineered even the un-milled and un-shaped cores had been. Every Blizzard ski with True Mix requires its personal cocktail of woods (which may even differ by measurement), that means a single core consists of a number of wooden varieties in varied preparations.



Greater than a dozen folks contact a Blizzard ski from begin to end. The method takes greater than per week for every pair of skis. Somewhat than feeling just like the model makes use of robots to construct skis, I left the manufacturing facility feeling prefer it’s laborious to not name Blizzard a “handmade” ski firm.

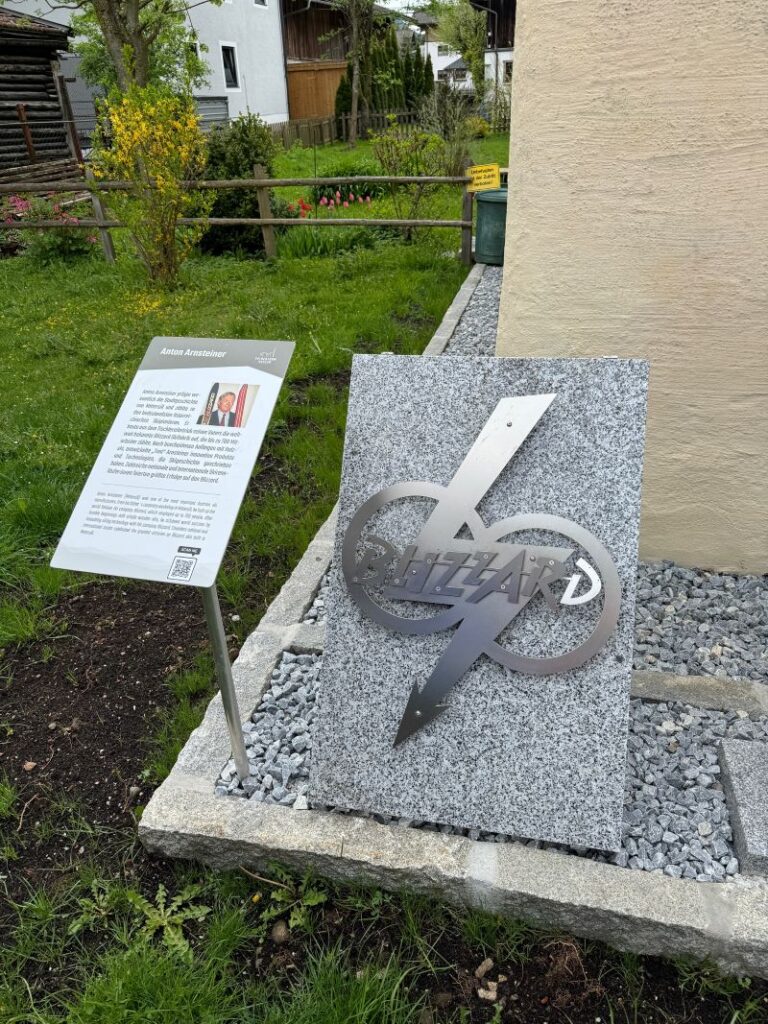
Feedback